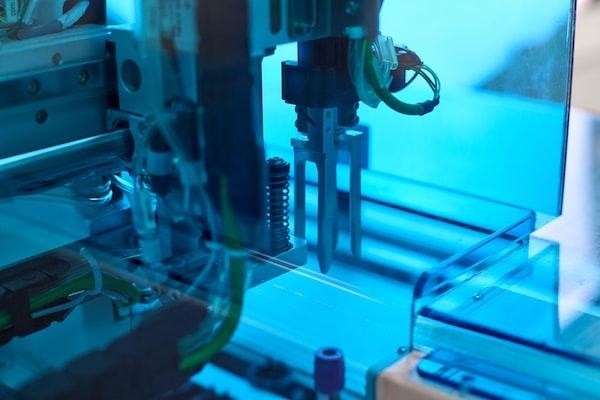
There are many factors to consider when it comes to managing equipment. This article will provide a few tips to keep in mind when trying to optimize your process. Keep reading to learn more about effective ways to manage equipment.
Using Equipment Management Software
Equipment management software is a program that helps businesses track and manage their equipment. This software also creates detailed reports on all equipment in a business’s inventory. There are many benefits to using equipment management software.
One of the most significant advantages is that it can help businesses save money. Equipment management software help companies keep track of their assets, so they don’t accidentally lose any expensive equipment. It also allows businesses to schedule regular maintenance for their equipment, which can help prevent costly repairs down the road. Additionally, with up-to-date information on warranties, companies can avoid paying for out-of-pocket repairs if something goes wrong with one of their machines. Overall, using equipment management software is a great way to keep track of all the different pieces of machinery in a business’s inventory.
Creating an Inventory of All Equipment
An inventory of all equipment is an essential step in effective equipment management. Your equipment management inventory should be formatted in a way that is easy to read and understand. This inventory should include information on each piece of equipment, such as make, model, and serial number. You should also list the date of acquisition, the purchase price, and the current value. If you have any manuals or other documentation for the equipment, you should also include that.
The inventory should also list where the equipment is located and who is responsible for it. This information helps to keep track of equipment locations, check equipment status, and plan for equipment replacement. You should keep your inventory up to date, noting any changes in the equipment’s make, model, or serial number. You should also note any changes in the purchase price or the current value.
If you sell or donate any equipment, you should update your inventory to reflect that. Having an up-to-date equipment management inventory is an essential part of your business.
Inspecting and Cleaning Equipment Regularly
Assuming your equipment is properly functioning is the first mistake people make when it comes to equipment management. Unfortunately, a lot can go wrong if the equipment isn’t properly taken care of. Dust, dirt, and other particles can quickly get inside the machine and cause it to malfunction. To ensure your equipment is functioning correctly, it is essential to inspect and clean it regularly. Cleaning the equipment is a relatively straightforward process.
Start by inspecting the exterior of the machine for any damage. Once you’ve verified that the machine is physically intact, move on to the interior. Look for any signs of wear and tear, especially around the filters and other sensitive areas. If you find any damage, report it to the manufacturer immediately. By taking these simple steps, you can help prevent equipment malfunctions and extend the life of your investment.
Organizing Equipment by Function
Another way to effectively manage equipment is to organize it by function. This means separating the equipment into categories based on how it is used. When organizing your equipment by function, it is essential to be as specific as possible. For example, you might want to create separate categories for hand tools and power tools. Or you might want to create categories for vehicles based on their sizes, such as small cars, large cars, and trucks.
The advantage of organizing equipment by function is that it makes it easier to find what you need. If you are having trouble organizing your equipment by function, you might try using a categorization tool. This tool allows you to create specific categories for your equipment and then save those categories in a database.