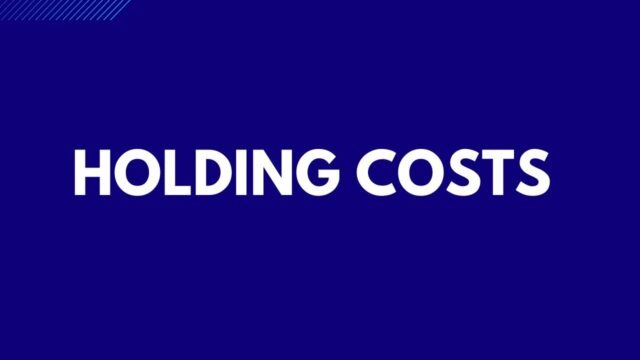
What are holding costs and why do they exist
Holding costs are the costs associated with storing inventory. They can include storage fees, insurance, and loss of interest on the money that is tied up in inventory. While holding costs are a necessary part of doing business, they can also cut into profits if they are not carefully managed.
One way to reduce holding costs is to keep inventory levels low. This can be accomplished by offering just-in-time delivery or by only stocking items that are likely to sell quickly. Another way to reduce holding costs is to negotiate better terms with suppliers. For example, you might be able to get a discount for paying early or for larger orders. By carefully managing holding costs, you can help ensure that your business remains profitable.
How to calculate holding costs
The formula for calculating holding costs is relatively simple: (average inventory value x annual carrying cost rate) / number of days in the year. However, there are a few important factors to keep in mind when using this formula. First, the average inventory value should be based on the value of the goods at the end of the accounting period.
Second, the annual carrying cost rate should include all costs associated with storing and managing inventory, such as warehouses rent, insurance, and taxes. Finally, the number of days in the year should be adjusted for any seasonal fluctuations in demand. By taking these factors into account, businesses can get a more accurate measure of their holding costs and make better decisions about inventory management.
Factors that influence holding costs
There are a number of factors that can influence the holding costs of inventory. One of the most important is the length of time that the inventory is expected to be held. Generally, the longer an item is expected to be held, the higher the holding costs will be. Other important factors include the level of uncertainty about future demand for the item and the storage conditions required. In addition, costs such as insurance and taxes can also add to the holding costs of inventory. By taking all of these factors into account, businesses can develop a more accurate picture of their true holding costs.
Methods for reducing or eliminating holding costs
Holding costs are the costs associated with holding inventory, and can represent a significant expense for businesses. However, there are several methods that businesses can use to reduce or eliminate these costs. One way to reduce holding costs is to implement just-in-time (JIT) manufacturing, which minimizes the need for inventory by aligning production with customer demand.
Another approach is to use forecasting techniques to more accurately predict future demand, which can help reduce the amount of safety stock that needs to be carried. In addition, businesses can also use inventory management software to track inventory levels and quickly identify when reordering is necessary. By implementing one or more of these strategies, businesses can significantly reduce their holding costs.
Examples of how companies have incurred holding costs
There are many examples of how companies have incurred holding costs. One common example is when a company stockpiles inventory in anticipation of future demand. This can tie up a significant amount of capital, and if the demand never materializes, the company is stuck with the inventory and the holding costs. Another example occurs when a company owns a fleet of vehicles that are used for business purposes. The vehicles must be stored, maintained, and insured, which all incur holding costs. Finally, companies often incur holding costs when they own real estate that is not being used. The property must be cared for and taxes must be paid, even though it is not generating any revenue. All of these are examples of how companies can incur holding costs.
The impact of holding costs on businesses and consumers
The impact of holding costs can be significant for both businesses and consumers. Holding costs are the costs associated with storing inventory, and they can include things like storage fees, insurance, and taxes. For businesses, holding costs can add up quickly, eating into profits and making it difficult to keep prices competitive. For consumers, higher prices can result from businesses passing on their increased costs. In addition, shortages can occur when businesses are unable to maintain enough inventory to meet demand. As a result, it is important to consider the impact of holding costs when making decisions about production and pricing.