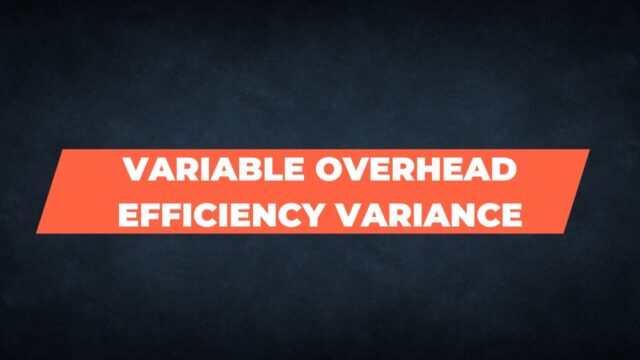
How Does Variable Overhead Efficiency Variance Affect Your Overhead Rate?
There are two forms of overhead rate variation: Fixed overhead rate variance and Variable Overhead Efficiency. These variances refer to the difference between the costs of fixed and variable overhead, respectively. It is important to understand the differences between these two kinds of variances and how they are calculated to improve overhead efficiency. Let’s look at the Variable Overhead Efficiency Variance. How does it affect your overhead rate? Which is better – Fixed overhead rate variance or Variable overhead rate variance?
Fixed overhead efficiency variance
In production, fixed overhead efficiency variance can be a good or a bad thing. A favorable variance means that more finished goods were produced within the same amount of time as planned. An unfavorable variance means that input labor hours were higher than the standard. In the last two examples, a variance of -50% means that more work was done in less time than planned. When a variance exceeds -50%, corrective measures need to be taken.
A variable overhead efficiency variance rises proportionately to the output. This variance reflects the difference between the standard cost of overheads allowed for the output and the actual cost incurred. Variable overhead variance is calculated separately for direct and overhead variable expenses. If the variance is high, the cause of the variance can be attributed to a price variance. For example, ABC Inc.’s factory used 28,000 hours of direct labor to produce its finished goods, resulting in a variable overhead variance of 5%.
A variable overhead efficiency variance is derived by using inputs from different departments. Production staff submits production expense information, while staff responsible for industrial engineering estimates the number of labor hours required to meet the output requirements. These estimates are based on historical employee productivity, capacity levels of equipment, and depreciation. The variance is then multiplied by the standard absorption rate for the same number of hours. The resulting number is known as the fixed overhead efficiency variance.
Overhead efficiency variance is a measure of the standard cost of manufacturing units divided by the actual hours. The standard cost is the total number of units produced minus the hours actually spent on production. Overhead efficiency variances are used to determine whether the factory is operating efficiently or not. They can be calculated in many ways. For example, if a manufacturing company allocates seven hours per day to overhead, the fixed overhead efficiency variance would be 87,200, while the standard cost is $4,800.
Variable overhead rate variance
Considering how variable overheads vary from month to month, it is necessary to know what the factors are that contribute to this variation. Variations in variable overheads may arise due to changes in the prices of underlying components, a discount on bulk orders, and indirect labor bonuses. Indirect labor expenses are also affected by accounting errors, as they are paid overtime for work performed on the job. Ultimately, the total variable overhead variance is the sum of the variable overhead rate variance and the variability of the productive efficiency.
One major concern that affects variable overhead efficiency is the margin of error associated with the standard labor hours. It is necessary to consider the validity of the underlying standard when determining the variance. For example, a company may determine that production staff work an average of 10,000 hours each month, while incurring variable overhead costs of $100,000 per month. The cost accounting staff may use this information based on historical labor patterns and may not be accurate.
The standard variable overhead rate is 9.40 per direct labor hour, while actual variable overhead rates are 8.30. The difference between the standard variable overhead rate and the actual variable overhead rate is one cent per hour. Therefore, a positive variance will result in favorable variable overhead spending, while a negative variance will likely produce negative results. Both are unfavorable and usually affect the production department. When the standard variable overhead rate is $9.40 per direct labor hour, a company must divide this number by actual labor hours to find the variable overhead rate.
The variable overhead rate variance is a comprehensive list of all production costs and labor hours that vary with changes in other variables. These costs are often unrelated to unit costs and can be a very valuable indicator when comparing different accounting methods, evaluating new suppliers, or examining the costs of different production processes. In fact, many companies use both labor and machine hours to determine their variable overhead rates, making it more important than ever to understand them.